Supply chain management in the energy industry faces significant hurdles, including rising material costs, logistics complexities, supply chain disruptions, and emission reduction pressures. These challenges are intensified by renewable energy transitions, data visibility issues, and the need to balance economic viability with environmental goals. Companies struggle with implementing energy efficiency measures across global supply networks amid strict decarbonization requirements.
Rising Costs and Resource Constraints in Energy Supply Chains
The energy industry supply chains are experiencing unprecedented cost pressures. According to Willis Towers Watson (WTW) report, the rising prices of raw materials combined with increasing labor costs are severely impacting income and growth potential for energy companies.
These escalating costs create significant barriers to entry for new projects and limit expansion capabilities for existing operations. For renewable energy specifically, material costs have become a critical concern as companies struggle to maintain profit margins while transitioning to greener operations.
Supply chain leaders across hydro, solar, wind, biofuels, geothermal, and battery storage sectors report that volatile energy prices further compound these challenges, creating a complex economic environment that threatens future investment capacity in the industry. These cost constraints directly affect the ability of companies to implement innovative supply chain solutions.
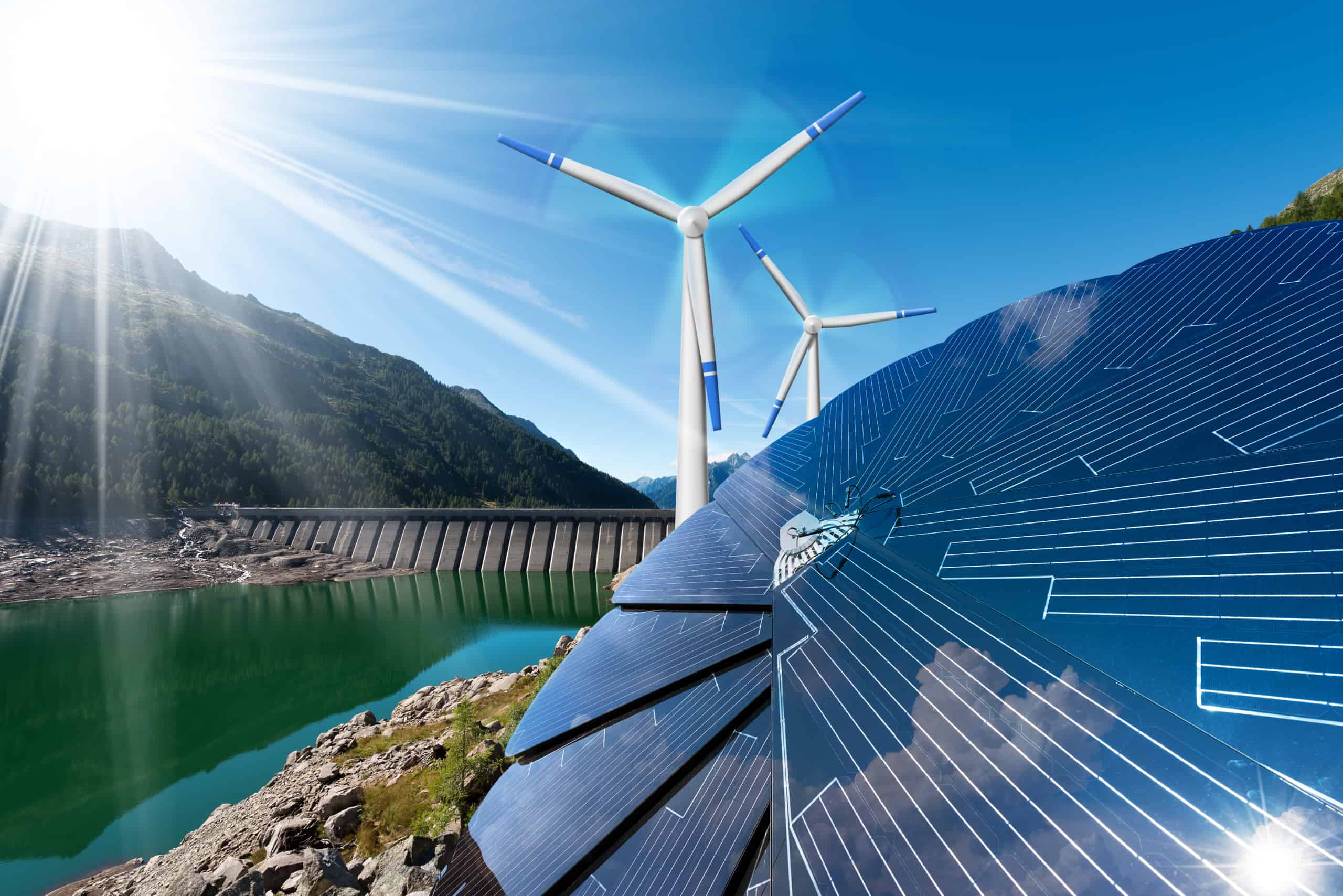
Supply Chain Disruptions and Operational Bottlenecks
Energy supply chains face frequent disruptions that compromise operational efficiency and project timelines. Shortages of critical components, manufacturing delays, and global logistics bottlenecks have created significant challenges for energy companies attempting to maintain consistent operations.
The complex interdependencies within energy supply chains mean that disruptions in one area can cascade throughout the entire system, amplifying negative impacts. Companies report that these bottlenecks create unpredictable lead times and inventory management challenges, forcing operations to maintain larger buffers that increase carrying costs.
- A 30% increase in disruptions was noted in the first half of 2024, with 10,629 documented cases reflecting heightened risks.
- The average response time to these disruptions is around 2 weeks, indicating potential bottlenecks in operational response mechanisms.
- Regulatory changes saw a 185% increase, suggesting compliance could create operational hurdles.
- Labor disruptions rose by 42% in the same period, likely contributing to production and logistics bottlenecks.
- Extreme weather events, up by 130% last year, have disrupted supply chains, potentially leading to capacity and operational constraints.
Logistics Planning and Transportation Efficiency
Logistics planning presents unique challenges for energy supply chains, particularly for new energy sources with transportation requirements different from those of traditional fuels. Research shows that effective logistics planning can reduce transportation time by approximately 20%, improve transportation efficiency by 15%, and decrease traffic congestion avoidance rates by 10%.
New energy supply chains face specific challenges related to limited energy storage capabilities and shorter transportation distances compared to conventional energy sources. Logistics planners must account for numerous intervention factors, including traffic congestion, traffic lights, and path angles, to optimize routes effectively.
Through logical analysis methods and careful planning, companies can realize significant cost savings. Effective logistics planning must balance cost reduction goals with environmental objectives, creating transportation networks that minimize both expenses and carbon footprints while maintaining reliable service levels.
Energy Efficiency and Scope 3 Emission Reduction
The energy industry faces immense pressure to improve efficiency and reduce emissions across entire supply chains. Industry data reveals that the sector was responsible for emitting 9.0 Gt of CO2, representing 25% of global emissions, while consuming 37% of global energy.
A critical challenge is addressing not just direct emissions but also scope 3 emissions from upstream suppliers, which research indicates can contribute more than 80% of total energy use in many manufacturing sectors. Despite energy efficiency being a cost-effective means to reduce CO2 emissions, few studies have adequately addressed energy efficiency within Supply Chain Management (SCM).
Most assessments examine only total energy use without exploring opportunities for reduction at the process level. Companies struggle to implement energy efficiency measures due to various barriers, including limited capital, inadequate expertise, and competing priorities. Developing comprehensive approaches to energy management that span organizational boundaries represents one of the most significant challenges facing energy supply chain managers today.
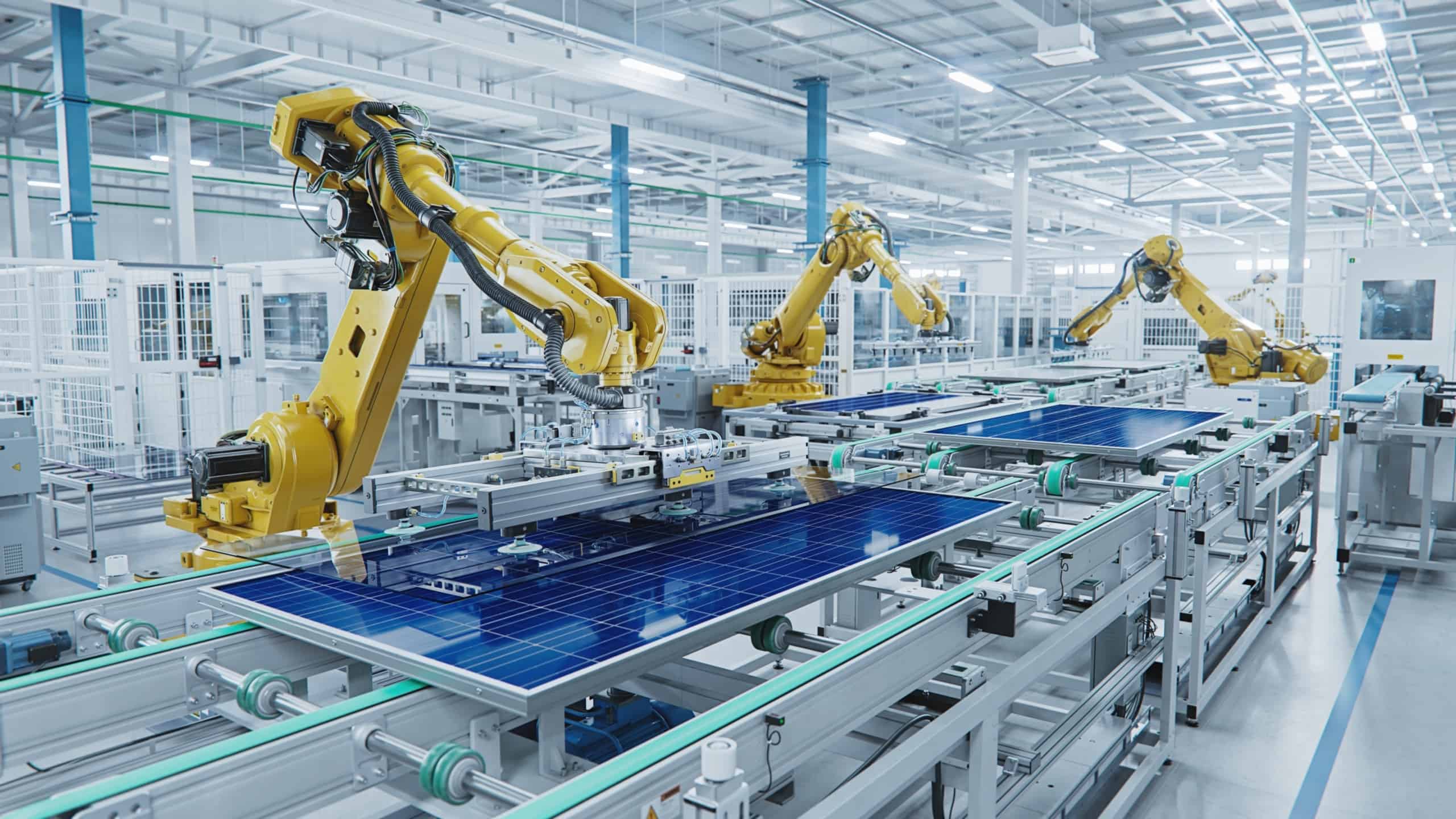
Data Visibility and Supplier Performance Assessment
Energy companies face substantial challenges in acquiring accurate, comprehensive data across multi-tier supply chains. Research indicates a significant lack of visibility beyond first-tier suppliers, making it challenging to assess environmental performance and identify improvement opportunities.
Obtaining reliable energy use data from outsourced activities presents consistent difficulties. Without process-level energy information, companies cannot identify potential areas for improvement or effectively track progress toward efficiency goals. Different measurement methodologies across organizations further complicate data consolidation efforts.
Data Visibility Challenges
- 24% of IT professionals cite a lack of visibility into sensitive data as their top data security challenge.
- According to Agility PR, 57% of organizations, including energy companies, report new systems containing user data are added weekly or daily, compounding visibility issues.
- 90% data sparseness (missing or incomplete data) reduces supply chain visibility to 52% for noise, 65% for bias, and 32% for missing values.
Challenges of Supplier Assessment
- Barriers include data availability/accuracy, lack of standardized metrics, dynamic market conditions, and limited visibility into supplier operations.
- A UK-based case study highlights the need to balance manufacturing and energy companies’ and suppliers’ perspectives in performance evaluations.
- Efficiency and transparency in supplier assessments reduce procurement time and improve decision-making confidence.
- Supplier Performance Management (SPM) frameworks emphasize consistent measurement, evaluation, and improvement of supplier performance.
Standardization Challenges in Energy Assessment
A significant obstacle for energy supply chains is the absence of standardized methods for assessing supplier energy performance. Studies reveal a lack of consistent frameworks and metrics for evaluating energy efficiency across different organizations and sectors.
Likewise, this standardization gap makes meaningful comparisons between suppliers nearly impossible and complicates target-setting and performance-improvement initiatives. Small and medium-sized enterprises (SMEs) face particular difficulties implementing energy management systems without clear guidelines or assessment methodologies tailored to their capabilities.
The heterogeneity of industrial processes compounds this challenge, with specialized operations requiring customized assessment approaches rather than one-size-fits-all solutions. Energy-intensive processes vary significantly across different manufacturing sectors, necessitating industry-specific taxonomies and key performance indicators (KPIs).
Without standardized assessment frameworks, companies struggle to integrate energy efficiency considerations into supplier selection and management processes, limiting progress toward comprehensive supply chain decarbonization.
Renewable Energy Supply Chain Transformation
- Raw material shortages, logistical hurdles, and financial constraints disrupt renewable energy supply chain efficiency.
- Wind capacity additions fell 14% to 2.6 GW in 2025 due to supply chain bottlenecks and financing delays.
- Global renewable energy capacity will grow by 2.5x by 2030, intensifying grid infrastructure demands.
- Global electricity generation reached 29,925 TWh last year, driving urgent renewable energy adoption.
- Fossil fuel price volatility (5x to 7x fluctuations) undermines renewable energy supply chain stability.
- Solar PV, wind turbine, and battery manufacturing value chains face scaling complexities amid rising demand, according to a recent report.
- Supply chain pressures and energy uncertainty reduce renewable energy stock returns by 15% to 20%.
- Firms struggle to integrate low-carbon practices into supply chains despite renewable energy investments.
- Permitting delays and regulatory hurdles slow renewable project deployment, exacerbating capacity gaps.
- Digitalization mitigates supply chain disruptions but requires 30% to 40% more investment for renewable resilience.
The transition to renewable energy sources introduces distinct supply chain challenges that threaten to impede the global shift away from fossil fuels. Recent research demonstrates that renewable energy supply chains face pressure from material shortages, logistics constraints, and geopolitical factors that impact project viability.
Solar, wind, and battery storage technologies rely on specific raw materials with concentrated supply sources, creating vulnerability to disruptions. Supply chain bottlenecks in manufacturing critical components like energy storage systems, solar panels, wind turbines, etc., directly affect project timelines and costs.
Renewable energy infrastructure requires substantial upfront investment in new manufacturing capabilities, distribution networks, and installation expertise. Companies must simultaneously dismantle legacy fossil fuel supply chains while building entirely new systems for renewable energy sources, which is a complex transition that strains organizational resources and capabilities.
Without careful management of this transformation, the renewable energy sector risks failing to scale at the pace required to meet global climate goals despite strong market demand and policy support.
Financial Viability and Investment Challenges
Maintaining financial viability while transforming energy supply chains presents significant challenges for industry participants. Many energy companies struggle to justify the upfront investments required for sustainable supply chain transformations despite long-term benefits.
Innovative financing approaches like financial collaboration between supply chain members can help overcome these barriers, mainly when larger focal companies with access to capital invest in improving supplier energy efficiency. In some cases, it may be more beneficial for focal companies to invest in enhancing supplier energy performance than making equivalent investments in-house.
Energy companies must carefully balance short-term financial performance with long-term sustainability objectives while navigating changing market conditions, regulatory requirements, and investor expectations regarding environmental performance.
Strategies for Building Resilient Energy Supply Chains
- Reshoring and near-shoring reduce reliance on distant suppliers, minimizing geopolitical and logistical risks.
- Digitalization tools (e.g., IoT, AI) enhance supply chain visibility and predictive maintenance capabilities.
- Supplier diversification mitigates disruption risks from over-reliance on single sources.
- Sustainability integration aligns procurement with low-carbon goals, improving long-term resilience.
- Asset-light solutions (e.g., third-party logistics) reduce capital expenditure and operational rigidity.
- Flexible transportation networks enable rapid rerouting during disruptions.
- Inventory buffer strategies ensure critical component availability during supply shocks.
- Long-term supplier partnerships improve communication and on-time delivery reliability.
- Supply chain mapping identifies vulnerabilities in energy component sourcing and distribution.
- Alternate sourcing routes for rare earth materials reduce dependency on high-risk regions.
- Real-time data analytics optimize energy supply chain responsiveness to demand fluctuations.
- Streaming agreements with advance payments secure priority access to critical renewables components.
- Cross-sector collaboration (utilities and manufacturers) accelerates decarbonization and innovation.
- Visibility, flexibility, collaboration, and control are foundational pillars for resilient energy operations.
- Redundancy in supplier networks safeguards against single points of failure in solar/wind projects.
- Adaptive planning frameworks enable rapid response to policy changes or material shortages.
- Renewable energy deployment grew significantly, reducing fossil fuel dependency.
- Decarbonization technologies (e.g., hydrogen, CCS) enhance energy system resilience.
- Risk assessment protocols align supply chain strategies with climate and geopolitical scenarios.
- Stakeholder-aligned KPIs (e.g., carbon footprint, lead times) drive accountability in energy transitions.
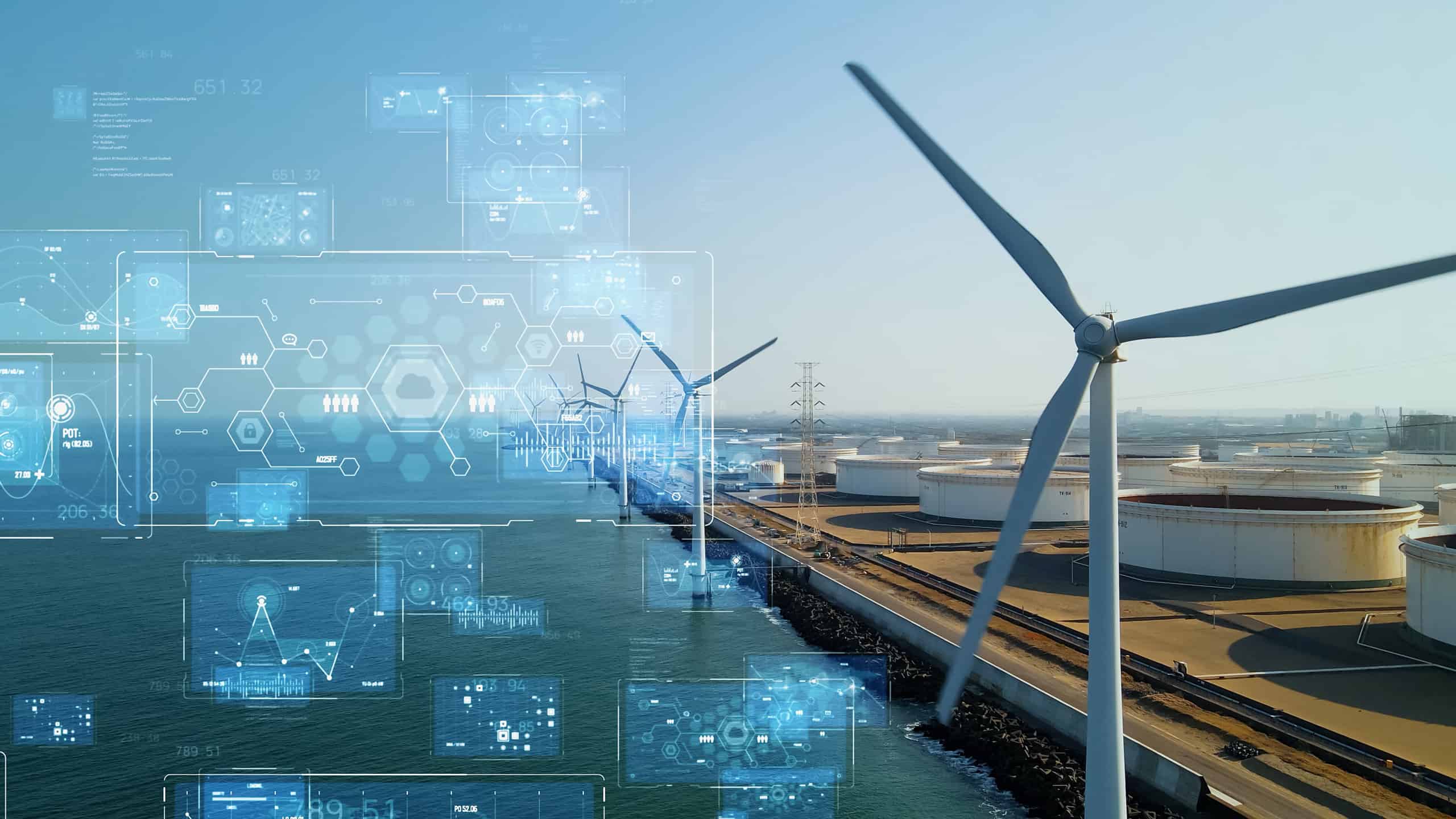
Final Words
Supply chain management in the energy industry faces multifaceted challenges requiring integrated solutions. Companies that successfully navigate these challenges will build resilient, sustainable supply chains capable of supporting the energy transition while maintaining economic viability. As the industry continues evolving, developing comprehensive strategies that balance financial, operational, and environmental objectives will remain essential for long-term success.