Turning supply chain disruptions into opportunities for growth have become critical for manufacturing companies seeking to thrive in today’s volatile business environment. These disruptions, ranging from pandemics to extreme weather events and geopolitical tensions, force manufacturers to rethink operations, adapt quickly, and find innovative solutions. Agile companies use these challenging moments to strengthen their position, improve processes, and discover new revenue streams that might otherwise remain unexplored.
Modern Supply Chain Disruptions in Manufacturing
Transforming supply chain disruptions into opportunities for growth begin with a clear understanding of what today’s manufacturers face. Modern manufacturing companies deal with unprecedented challenges that affect their ability to source materials, produce goods, and deliver products to customers.
Recent years have shown how vulnerable global manufacturing supply chains can be. The semiconductor industry, for example, faces manufacturing cycle times ranging from 50 to 100 days with operations running 24/7, making it particularly susceptible to external shocks.
These disruptions lead to production backlogs, inventory problems, and significant price pressures on both inputs and outputs. Common supply chain disruptions affecting manufacturers include:
- Extreme weather events are damaging infrastructure and halting transportation
- Geopolitical tensions and wars are disrupting international trade routes
- Transportation disruptions leading to logistics bottlenecks
- Supply-demand imbalances create inventory challenges
The impact of these disruptions expands beyond immediate operational issues. Production backlogs continue to pile up, putting pressure on input and output prices. Smaller suppliers with limited pricing leverage often bear the brunt of escalating costs. Cash-flow pressures compound market uncertainties, slowing investment in new capacity and creating a cycle of supply chain vulnerability.

How Supply Chain Disruptions Create Growth Opportunities
Supply chain disruptions transform into opportunities for growth when companies shift their perspective from crisis management to strategic advantage. Instead of merely surviving disruptions, forward-thinking manufacturers use these moments to reimagine their operations and position themselves for future success.
The automotive industry provides a compelling example. When chip shortages severely impacted global automobile production, companies were forced to evaluate their supply chain strategies.
Some manufacturers used this moment to develop new supplier relationships, create more reasonable procurement mechanisms, and even promote independent research and development of chips. These moves strengthened their competitive position beyond the immediate crisis.
Research shows that disruptions often reveal opportunities that would otherwise remain hidden during normal operations. Production slowdowns give companies time to evaluate inefficiencies, while supply shortages can spur innovation in materials and design.
Reshaping Supplier Networks
As stated earlier, disruptions highlight weaknesses in supplier networks that might go unnoticed during normal operations. Smart manufacturers use these insights to build more resilient supplier relationships. Effective approaches include:
- Supplier diversification across geographic regions
- Near-shoring critical component production
- Strengthening supply chain cooperation through transparent communication
- Establishing backup suppliers for critical components
- Creating flexible contracts that adapt to disruption scenarios
Companies implementing these strategies report not just improved resilience but often find cost savings and quality improvements through better supplier relationships.
Accelerating Digital Transformation
Disruptions frequently accelerate digital adoption as manufacturers seek solutions to operating with limited resources or remote workforces. The transition from Industry 4.0 to Industry 5.0 technologies has been accelerated by recent supply chain challenges.
Technologies that were once considered optional have become essential for companies looking to maintain operations during disruptions. Important digital transformation opportunities include:
- AI-powered demand forecasting to anticipate market shifts
- Cloud-based supply chain management for remote visibility
- IoT sensors for monitoring of goods and equipment in real time
- Additive manufacturing (3D printing) for on-demand part production
- Digital twins to simulate and test supply chain scenarios
These technologies not only help navigate current disruptions but also position companies for long-term competitive advantage through improved efficiency and customer responsiveness.
Practical Strategies to Transform Disruptions into Growth
Turning supply chain disruptions into growth opportunities requires more than reactive measures. Manufacturers must develop systematic approaches to not just survive but thrive during challenging times. Strategic risk agility, the capacity to foresee and address risks proactively and flexibly, has become essential for manufacturing success.
Remember, this includes anticipating potential threats, evaluating their impact, and quickly adapting to changing conditions. Studies show companies with high strategic risk agility respond faster to disruptions and return to growth more rapidly than competitors.
Building Resilient Manufacturing Systems
System dynamics modeling helps manufacturers understand how disruptions impact their operations and identify intervention points for improved resilience. Effective approaches include:
- Scenario planning to prepare for multiple disruption types
- Capacity analysis across the entire supplier network
- Hidden factory effect evaluation to uncover operational blind spots
- Manufacturing yield impact assessment on supplier capacity
- Production system flexibility to adapt to changing conditions
Ford Motor Company, with 37 plants globally using 17 billion parts annually to manufacture six million vehicles, demonstrates the scale of this challenge. With up to ten supplier tiers between the company and raw materials, any disruption can cause substantial financial losses, making early identification of problems critical.

Leverage Technology for Supply Chain Optimization
Advanced technologies offer powerful tools for transforming disruptions into growth opportunities. A model-based multi-agent framework enables dynamic decision-making and coordination among supply chain partners during disruptions. So, this approach allows for agile responses without requiring prior knowledge of specific disruption types.
Technology |
Disruption Application |
Growth Opportunity |
AI/Machine Learning |
Predict potential disruptions |
Proactive risk management |
IoT Sensors |
Real-time supply chain visibility |
Inventory optimization |
Blockchain |
Supply chain transparency |
Improved supplier trust |
Digital Twins |
Disruption scenario simulation |
Better contingency planning |
Advanced Analytics |
Pattern identification |
New market insights |
These technologies help manufacturers not only weather disruptions but also identify new market opportunities, optimize operations, and create competitive advantages that persist long after the disruption ends.
Measure Success: KPIs for Growth During Disruptions
To effectively turn disruptions into growth, manufacturers need clear metrics to monitor and assess the progress and measure outcomes. Key performance indicators should focus on:
- Operational resilience: time to recovery after disruption
- Supply chain visibility: real-time awareness of potential problems
- Supplier performance: reliability during challenging conditions
- Production flexibility: the ability to adapt to changing circumstances
- Financial impact: cost reduction and revenue protection
Research shows substituting goods in established supply chains is often more effective than creating new distribution links during disruptions. So, this substitution flexibility can be measured and improved over time, creating a valuable asset for managing future disruptions.
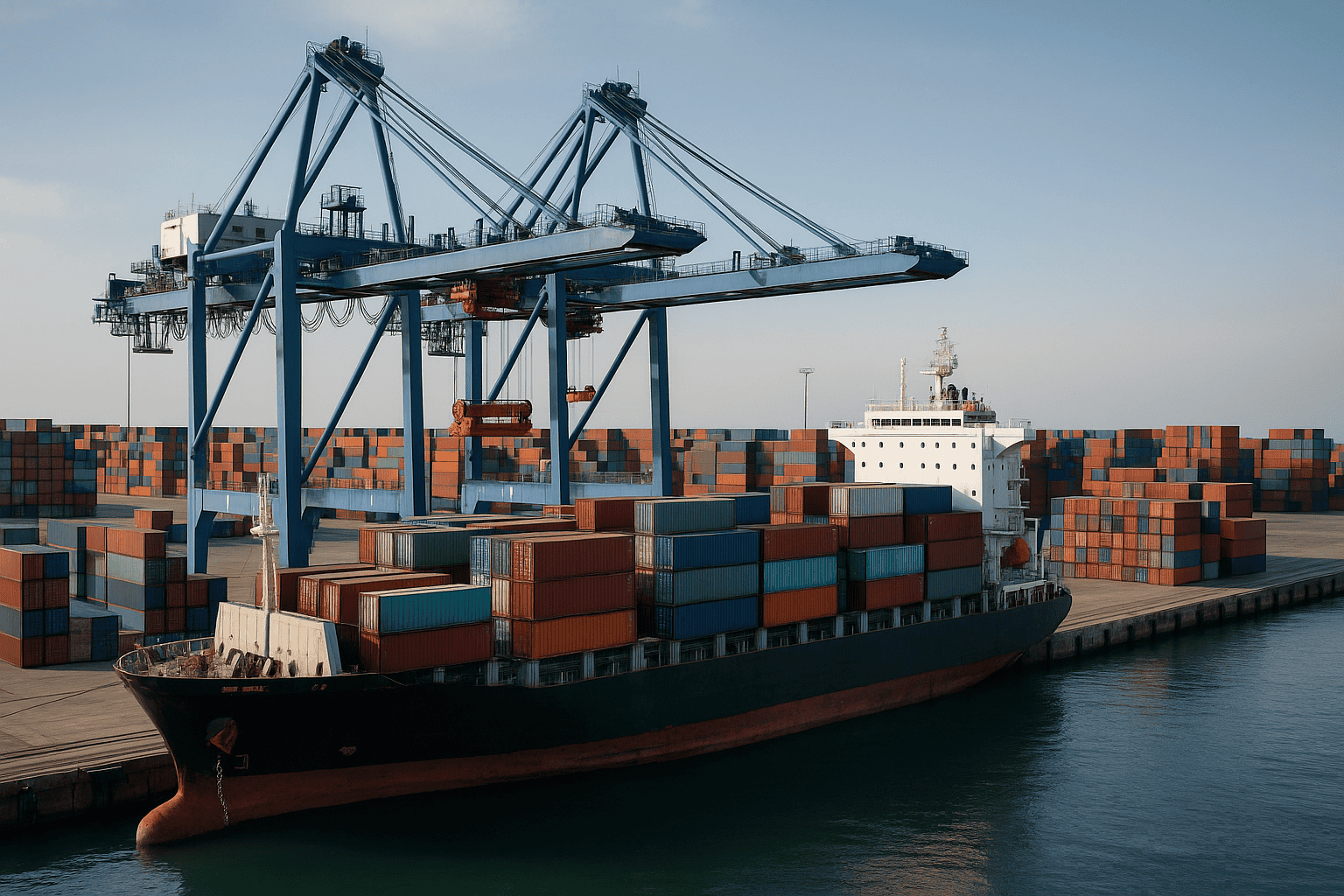
Prepare for the Next Supply Chain Disruption
The manufacturing sector continues to evolve toward highly integrated and autonomous production systems. A critical aspect of future-proofing is developing what researchers call “substitution flexibility,” which is the ability to use alternative materials, components, or processes when primary options are unavailable. Manufacturers looking to build long-term growth from disruptions should:
- Invest in early warning systems to identify potential disruptions
- Create standardized response protocols for different disruption types
- Develop continuous improvement frameworks focused on resilience
- Balance efficiency with redundancy in critical systems
- Explore Industry 5.0 technologies that integrate human capabilities with AI
The MARE framework offers a structured approach to examining the restoration of supply chain operations after disruptions. Likewise, this framework helps identify measures to enhance integration and increase supply network resilience.
Final Words
Turning supply chain disruptions into opportunities for growth in manufacturing requires a fundamental shift in perspective. Rather than viewing disruptions as purely negative events, forward-thinking manufacturers recognize them as catalysts for positive transformation.
The companies that emerge strongest are those that use disruptions to accelerate digital adoption, strengthen supplier networks, and build more resilient operations. Implement strategic risk agility practices, leveraging advanced technologies, and measuring progress with appropriate metrics.
That way, manufacturers can not only survive disruptions but also use them as springboards for sustainable growth. As manufacturing continues to evolve toward more integrated and autonomous systems, the ability to transform disruptions into opportunities will become an increasingly valuable competitive advantage.